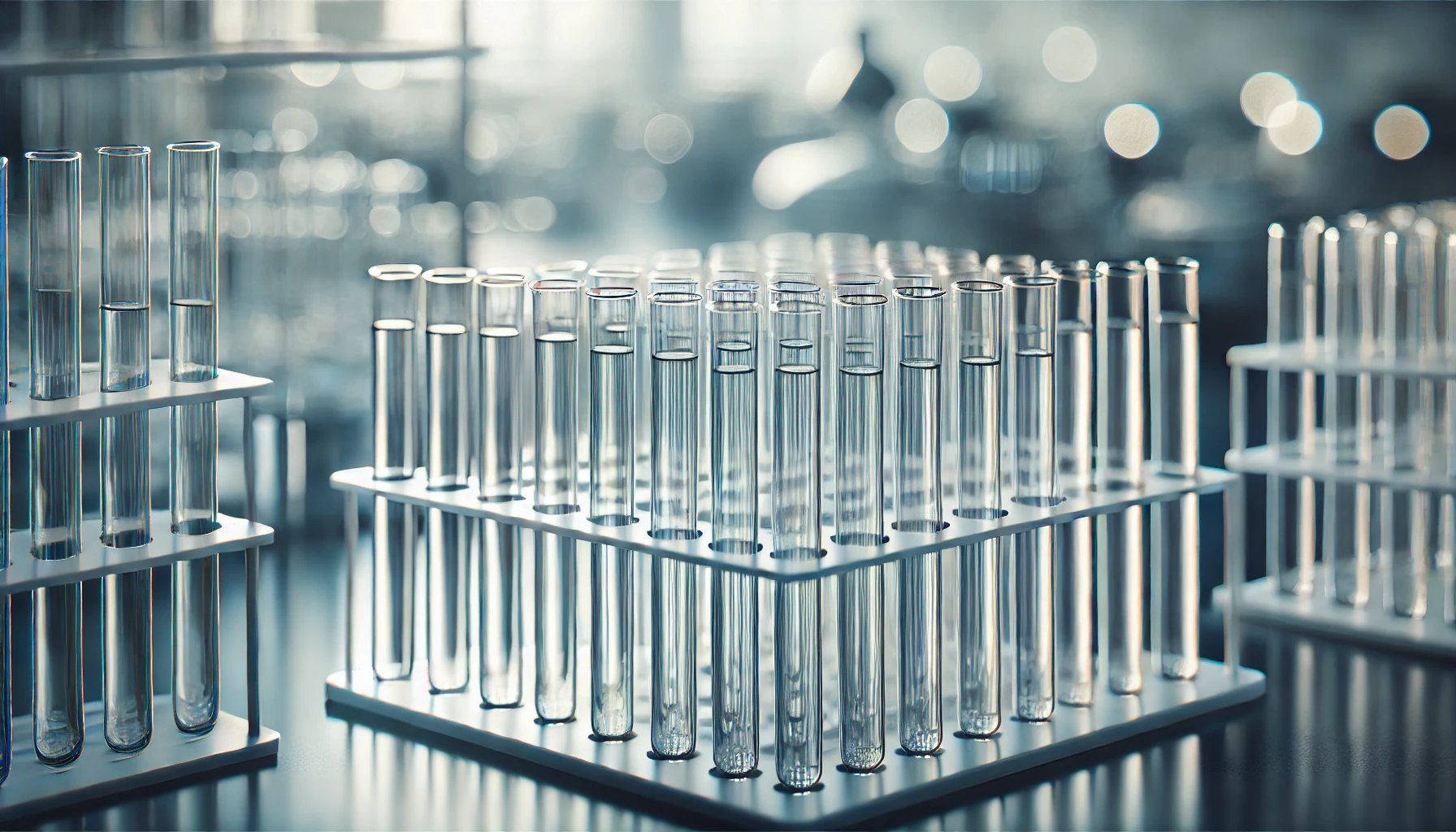
Ion Exchange For High Strength And Durability
Chemical strengthening involves immersing glass in a potassium salt bath where smaller sodium ions are replaced by larger potassium ions. This produces high surface compression which significantly improves strength and impact resistance. By extending product life and reducing the need for replacement, chemically strengthened glass supports sustainability. Its enhanced durability helps minimise waste and resource use, contributing to a more resilient and environmentally friendly product lifecycle.
Molten Salt For Chemical Strengthening Of Glass
Introducing our innovative salt melt medium, designed to improve the efficiency of the ion exchange process. This unique solution significantly reduces processing temperatures and times, enabling energy-efficient operations while maintaining high-performance outcomes.
Our technology lowers costs associated with energy consumption, it also improves the quality and consistency of the final product. With this new approach, your production processes can achieve greater efficiency and reliability, positioning your operations at the forefront of industry innovation. Embrace the future of ion exchange to provide thinner, stronger and lighter glass products.
Applications for strengthening glass
Faster processing times
Our technology enables faster processing by accelerating ion exchange and improves efficiency compared to slower thermal tempering.
Lower process temperatures
They offer lower process temperatures, which reduces thermal energy consumption and makes processing more environmentally friendly.
Extremely Durable, Extending Product Life-Cycles
Chemically strengthened glass delivers high robustness, enhancing longevity and reducing the need for replacements
Strongest glass products & scratch-resistant
It offers superior strength and outperforms thermally tempered glass in terms of impact resistance and durability.
Advantages of chemical strengthening compared to thermal tempering
Better process control
Provides better control over the level of surface compression, e.g. through engineering stress profiles (ESP), which ensure uniform depth over the entire surface, with temperature playing only a minor role compared to the results of thermal tempering.
Complex shapes & thin glass
It is suitable for complex shapes (round, flat, corners) and thin glass, in contrast to thermal tempering, which has difficulties with such specifications.